Staying in time – Data acquisition and transmission with R-Series V SSI (part 2)
What is the synchronous mode 2 on the R-Series V SSI?
In synchronous mode 2, the sensor adapts the execution of the measurement and the transmission of the position value to the polling cycle of the controller, as in synchronous mode 1. However, in synchronous mode 2 a new measurement is started when the last measured position value is queried by the controller. Since the measurement is started with the polling cycle of the control, this is also called "synchronous start". The advantage of synchronous start is that the user knows exactly how "old" the measurement is, i.e., when the measurement was started – namely at the last polling cycle (Fig. 1). During the execution of the measurement, the measured value is no longer updated. As with any synchronous measurement, the dead time is also constant in synchronous mode 2.
Fig. 1: Schematic representation of synchronous mode 2 for R-Series V SSI.
In Fig. 1, the polling cycle of the controller is so long that the sensor can perform the measurement at every cycle and provide a recent measured value. There are applications where the measured values are to be acquired at very short intervals. In addition, it must be considered that the time required by the sensor to perform a measurement and provide a measured value increases as the stroke length of the sensor increases. What happens if the polling cycle of the controller is shorter than the time needed by the sensor to perform a measurement?
Synchronous mode 2 with extrapolation
In addition to synchronous start, the synchronous mode 2 also includes linear extrapolation. Here, during the position measurement, a linear estimation about the movement of the position magnet is performed based on the previous data. Since the sensor knows the polling cycle of the controller and when the next position value will be requested, the sensor extrapolates the position of the magnet for the time of the next poll. In Fig. 2, the cycle time of the sensor is doubled compared to Fig. 1 and the polling cycle of the controller is shortened. After the sensor has synchronized to the polling cycle of the controller, the sensor provides a new measured value for each polling cycle due to the extrapolation, even if the cycle time of the sensor is longer than the polling cycle of the controller. With each determined measured value, a check and, if necessary, a correction of the linear extrapolation is carried out.
Fig. 2: Schematic representation of synchronous mode 2 for R-Series V SSI with extrapolation.
In this example the extrapolation enables the sensor to provide a new measured value at each polling cycle, independent of its stroke length. This is possible up to a polling frequency of 10 kHz. Without extrapolation, the last measured value would be reported repeatedly until a new measured value is determined.
The synchronous mode 2 is a combination of synchronous measurement with synchronous start and extrapolation. In synchronous mode 2, extrapolation is activated automatically by the sensor if the polling cycle of the controller is shorter than the cycle time of the sensor.
What is the synchronous mode 3 on the R-Series V SSI?
Like synchronous mode 2, synchronous mode 3 is a combination of synchronous measurement with synchronous start and extrapolation. This means that the measurement is started with the polling cycle of the control. Likewise, the sensor activates extrapolation when the control's polling cycle is shorter than the sensor's measurement cycle. The other feature of the synchronous mode 3 is the minimization of the lag error.
As described before, the measured value is no longer updated while a measurement is being performed. However, the position magnet often does not stand still, but continues to move during this time. This moving of the magnet is not considered by the sensor, because the sensor is busy performing the measurement. The time the sensor needs to perform the measurement and provide the measured value, the sensor "lags" behind the real position value. This lagging behind is called lag error or following error. This lag error is minimized in synchronous mode 3.
In Fig. 3, the cycle time of the sensor is 1.5 units of the control’s polling cycle. If the position magnet on the sensor moves at a constant velocity, the lag error is constant: In this example, this lag is 1.5 units of the polling cycle. Since the sensor knows by how many units it is lagging, it can take this into account when reporting the position value. In this example applies:
- For time 3: Output value = measured value at time 1 + lag error 1.5 units
- For time 4: Output value = measured value at time 1 + lag error 1.5 units + extrapolation
- For time 5: Output value = measured value at time 3 + lag error 1.5 units
- For time 6: Output value = measured value at time 3 + lag error 1.5 units + extrapolation
- For time 7: Output value = measured value at time 5 + lag error 1.5 units
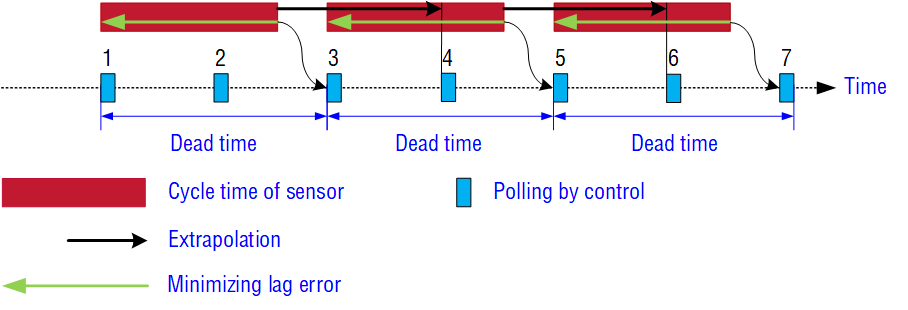
With a synchronous start as with synchronous mode 2, the user knows how "old" the measured value is, but this measured value is already "out of date" when it is reported. This is taken into account in synchronous mode 3 by minimizing the lag error. Thus, a measured value is reported from the sensor at the time of the polling, which is very, very close to the real position of the magnet at the time of this polling.
What does this mean for the application?
The different modes for data acquisition and transmission in the R-Series V SSI allow the user to select the timing of the sensor during measurement according to his application. The mode can be changed on-site using the TempoLink smart assistant. A measurement that takes place synchronously to the clock of the controller is an essential requirement for applications in which several axes are moved simultaneously. The synchronous start offers the advantage that the user knows exactly at which time the measured value was determined. In addition, the extrapolation makes it possible to provide a new measured value even if the sensor is polled by the controller in a shorter cycle than its measuring cycle. The R-Series V SSI thus makes it possible to always stay in time.
GET IN TOUCH WITH US
You have a question about one of our products or would like more details on a possible application?
Click here to fill in our request form
Don't want to miss out on the latest blog updates and other news?
Click here to subscribe to our newsletter
Total customer satisfaction
We live by the promise of unparalleled service that
enables us to take all available means to exceed your expectations.
Click here to find out how we support our customers