Position sensors optimize veneer peeling processes
Raute’s business is to create production solutions with maximum yield and optimal use of side products. Their machines and technologies serve the wood products industry worldwide by combining knowledge, digital innovation, and first-class service to create a sustainable future. Wood processing machinery include several machines and production lines, of which one of the most important is the veneer peeling line. A veneer peeling line comprises several parts: conveyors to bring in the blocks, charger to move the block in optimal position to lathe, which performs the actual peeling process, veneer conveyors to move the veneer ribbon to a clipper, which cuts it to sheets and finally a stacker to stack the veneer sheets. Sophisticated measuring and machine vision systems are used to guarantee high recovery when at the same time the block is peeled to veneer with high speed and accuracy.
Veneer-peeling-machine
Axis positioning with Temposonics®
Raute Oyj is using Temposonics® position sensors since the middle of the 1980s. Back then, they acquired a US company, which installed Temposonics® displacement transducers in the cylinders mounted on their machines. They basically inherited the sensors from the US company and started installing them into other veneer peeling applications. For example, the Veneer Peeling Line R7 uses about twenty position sensors in different measuring and motion control axes. The sensors must be fast to meet the requirements from fast movements to control loops.
“Some of position sensors are equipped with EtherCAT®, but the majority features SSI output,” explains Mr Pennanen. “In the past, we have used other sensor solutions, for example optical sensors, as well. However, when you consider the environment of the machine and how the material is prepared for the peeling process, the logical choice for us was going for magnetostrictive displacement transducers. ”Indeed, the typical environment for veneer peeling machines is dirty, warm, steamy, wet, and contains wood debris from the blocks. In addition to this, the sensor must withstand shocks and vibrations, which can happen for example when grabbing the block with spindles.
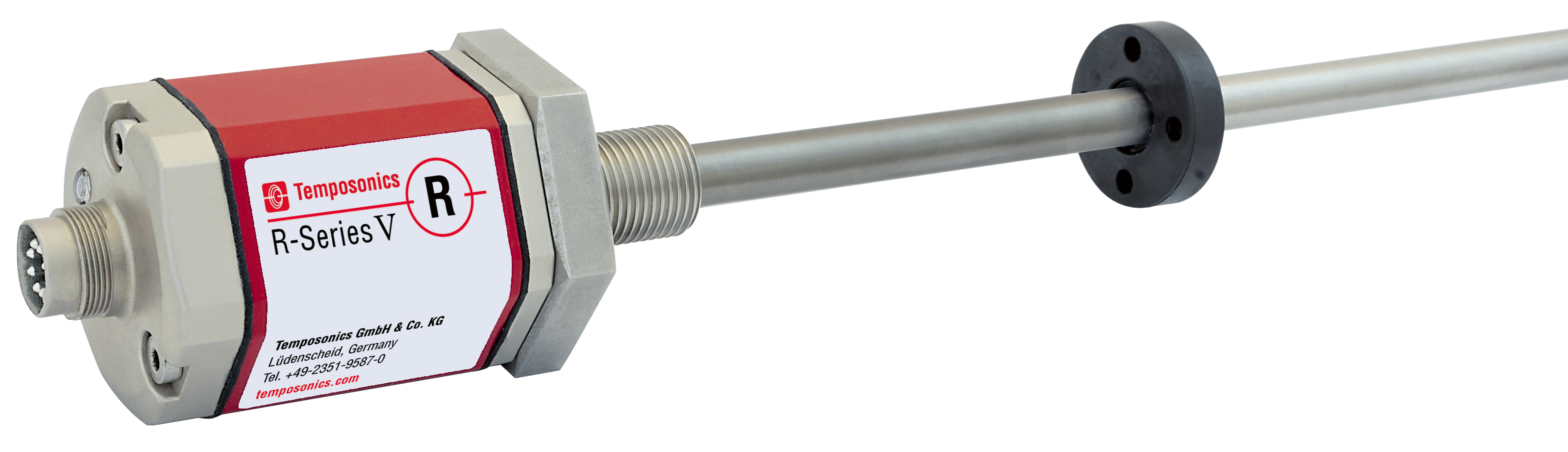
Temposonics® R-Serie V RH5 SSI
“We install R-Series RH position sensors in the hydraulic cylinders. The advantages of these transducers are the reliability and high accuracy. Although the position sensors are integrated in cylinder and so protected from the external environment, it was important for us that the sensors feature a high resistance towards shocks, vibrations, and high temperatures,” says Mr Pennanen and continues: “On top of that, a good service and, if necessary, fast support also play a key role, when we cooperate with a company which supplies parts for our machines.”
Veneer Peeling 4.0
Raute’s latest machines are made to meet the challenges of Industry 4.0. The system that Raute has implemented supports overall data collection from the application, such as movement cycles, wear and tear of the parts, counting of the blocks and other additional data. “We collect and provide this data to the customer. In this way, it is possible to plan maintenance cycles more efficiently, monitor the machine condition and get overall production monitoring. At the same time the data helps us to better understand the machine when it is operating on-site and to further develop future generations,” says Mr Pennanen and he continues to explain the advantages that Temposonics® R-Series V position sensors can bring to the machine. “The high reliability of the sensors together with the increased shock, vibration and temperature resistance guarantees that even when the application takes a harder hit, the position signal remains intact and keeps providing position feedback of the hydraulic cylinders. What we are really looking forward to is getting additional data from inside the cylinder, like temperature measurement or count of stroke movements and stroke distances. This additional information will improve our overall data collection, which in turn will lead to an increased performance of the peeling machine.”
Right now, Raute is testing the latest generation of R-Series position sensors in their veneer peeling test machines and once those tests are finalized, the machines will be sent out equipped with the newest Temposonics® sensors. “This will not only continue improving our peeling machines but also enable us to provide even more detailed information and advanced service to our customers and those are the key benefits of Industry 4.0,” closes Mr Pennanen.
GET IN TOUCH WITH US
You have a question about one of our products or would like more details on a possible application?
Click here to fill in our request form
Don't want to miss out on the latest blog updates and other news?
Click here to subscribe to our newsletter
Total customer satisfaction
We live by the promise of unparalleled service that
enables us to take all available means to exceed your expectations.
Click here to find out how we support our customers